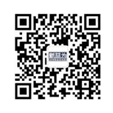
微信公眾號二維碼
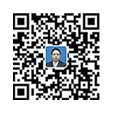
微信咨詢顧問二維碼
本文摘自以上書籍,作者:新益為
新益為精益生產(chǎn)咨詢公司概述:世界科技革命的浪潮,正在席卷著全球,科技進步的周期迭代,正在從百年一變、五十年一變,成為十年一變。近年來,以計算機技術(shù)和互聯(lián)網(wǎng)技術(shù)為牽引的新一代技術(shù)革命,已經(jīng)以五年為一代而飛速發(fā)展,核心技術(shù)理念及其應用的“三年迭代”,已經(jīng)成為各國科技研發(fā)的基礎(chǔ)坐標。
面對如此快速深化發(fā)展的現(xiàn)代技術(shù),面對如此海量的知識信息,傳統(tǒng)商業(yè)文明和商業(yè)模式框架,遭受了徹底的顛覆性沖擊,局部甚至是毀滅性的?;ヂ?lián)網(wǎng)改變了我們的生活和生產(chǎn),傳統(tǒng)實體經(jīng)濟和實體企業(yè)面臨生死抉擇。
信息化與精益生產(chǎn)
近年來,隨著現(xiàn)場改善的方法和理論不斷成熟與完善,國內(nèi)很多企業(yè)紛紛將精益生產(chǎn)方式作為提高企業(yè)競爭力的有效工具,但國內(nèi)學術(shù)界和企業(yè)界對精益生產(chǎn)方式的研究與總結(jié)卻遠遠落后于美國等西方國家。
企業(yè)管理現(xiàn)狀和信息化應用現(xiàn)狀企業(yè)的生產(chǎn)任務的主要來源可歸納為:ERP發(fā)出的推式零組件生產(chǎn)計劃;由裝配環(huán)節(jié)發(fā)出的零組件拉式需求看板;企業(yè)內(nèi)部各個制造單元之間的單工序協(xié)作計劃。計劃員根據(jù)生產(chǎn)計劃及生產(chǎn)準備情況編制季度、月度生產(chǎn)計劃、周計劃和日班產(chǎn)計劃,并通過信息化系統(tǒng)或手工下達生產(chǎn)計劃。
車間信息化管理弱點:
工藝數(shù)據(jù)不準確、存在缺失現(xiàn)象,且工序沒有與設備、工裝工具等信息關(guān)聯(lián)。
現(xiàn)場采集不及時,存在計劃員代替工人操作開工、完工的情況,且系統(tǒng)內(nèi)班產(chǎn)完成情況也不好。
工時數(shù)據(jù)不準確,無法依據(jù)信息化系統(tǒng)計算工時。
不能及時反映設備信息。工序、人、設備等信息沒有關(guān)聯(lián)起來,計劃員進行派工,工人進行開工、完工等操作時,系統(tǒng)不能讀到設備的信息,“設備監(jiān)控”功能沒有發(fā)揮作用。
企業(yè)結(jié)合信息化系統(tǒng),推進精益管理的具體方法如下:
1、結(jié)合企業(yè)實際,升級信息化系統(tǒng)
結(jié)合企業(yè)實際升級信息化系統(tǒng)考慮到企業(yè)精益管理現(xiàn)狀及信息化系統(tǒng)與ERP、PDM、DNC等系統(tǒng)之間的集成,必須對原有信息化系統(tǒng)進行升級,升級后的信息化系統(tǒng)包括基礎(chǔ)數(shù)據(jù)管理、計劃管理、作業(yè)過程管理、質(zhì)量作業(yè)管理、工具工裝管理、設備維修管理、機床監(jiān)視與控制、可視化管控、系統(tǒng)管理九個子系統(tǒng),重要接口包括與PDM的產(chǎn)品和工藝數(shù)據(jù)接口、與ERP目前的工單數(shù)據(jù)接口、庫存數(shù)據(jù)接口、與DNC的基礎(chǔ)數(shù)據(jù)采集接口。
2、依托信息化系統(tǒng),限制過量生產(chǎn)
依托信息化系統(tǒng)限制過量生產(chǎn)用信息化系統(tǒng)進行季度計劃分解和生成月的零件投入產(chǎn)出計劃以及毛坯、原材料的需求計劃,控制生產(chǎn)的投產(chǎn)數(shù)量和時間,在保證配套交付的前提下實現(xiàn)“配套投入、最少投入、最晚投入”的精益理念。在精益管理過程中增加了一個車間訂單SO層次。
3、改進工序作業(yè)計劃管理過程
車間之間的零件轉(zhuǎn)移由車間訂單SO控制,從而加強對零件進出車間的橫向協(xié)同。根據(jù)考核計劃、毛坯供給狀態(tài)和設備工裝可用性情況,調(diào)整計劃,下達班產(chǎn),改善作業(yè)計劃的可行性和穩(wěn)定性,減少現(xiàn)場變化和頻繁分批的弊病。
改進工序作業(yè)計劃管理過程由生產(chǎn)線進行工序作業(yè)計劃的管理,包括領(lǐng)毛坯后將配套信息輸入系統(tǒng);開工、完工管理,關(guān)閉工序作業(yè)計劃和車間訂單;按照緊急任務調(diào)整工序作業(yè)計劃。在工序作業(yè)級設備和人員的派工過程中,以項目精益管理理論和約束理論為基礎(chǔ)優(yōu)化排序方法,重點保證瓶頸設備的高效和滿負荷運行。完善現(xiàn)行網(wǎng)絡計劃的編制機制,提高整個價值流生產(chǎn)線的利用率和生產(chǎn)計劃的穩(wěn)定性。
4、擴大系統(tǒng)應用范圍,完善基礎(chǔ)數(shù)據(jù)管理
擴大系統(tǒng)應用范圍,完善基礎(chǔ)數(shù)據(jù)管理為保證信息化系統(tǒng)數(shù)據(jù)的準確性,全面梳理信息化系統(tǒng)工藝路線數(shù)據(jù),重點針對與實際不符的工藝路線進行修正,完善基礎(chǔ)數(shù)據(jù),補全信息化系統(tǒng)工序信息中的設備、工裝工具信息。
將信息化系統(tǒng)基礎(chǔ)數(shù)據(jù)庫作為工廠人事、設備、工藝、工裝工具檔案,將操作者、設備、工序有機地關(guān)聯(lián)起來,進一步實現(xiàn)定人、定設備,重點設備加工固定產(chǎn)品,固化工藝參數(shù)及設備的經(jīng)濟批量。
5、實現(xiàn)進步信息可視化和在制品控制依托信息化系統(tǒng)
實現(xiàn)進度信息可視化和在制品控制依托信息化系統(tǒng)對計劃的各個層次包括整個零件的計劃——工作訂單、按車間進出的計劃——車間訂單以及每一道工序的作業(yè)計劃的進度實時采集,做到可視化。清晰的圖形便于計劃人員隨時根據(jù)企業(yè)計劃的改變進行督促和調(diào)整。通過對在制品的可視化監(jiān)控,扭轉(zhuǎn)在制品流轉(zhuǎn)過程中的擁堵現(xiàn)象。
6、實現(xiàn)全局設備狀態(tài)可視化管理
實行全局設備狀態(tài)可視化管理依托信息化系統(tǒng)建立設備管理臺帳,對設備進行狀態(tài)管理,對二保和三保的周期進行定義,由系統(tǒng)自動生成二保維修計劃,通過系統(tǒng)進行二保派工、記錄維修結(jié)果和狀態(tài)。對于設備的臨時故障維修,建立報警和響應機制,使信息傳遞速度加快并記錄響應時間,加強對機修人員的考核。在信息化系統(tǒng)平臺上進行設備可視化管理,用不同的顏色標注設備的運行狀態(tài),加工零件、操作者等信息,使現(xiàn)場設備生產(chǎn)工作更高效便捷直觀,下達生產(chǎn)作業(yè)計劃前,自動對設備進行可用性檢查,及時發(fā)現(xiàn)設備故障和短缺問題。關(guān)注設備的可用率和設備利用率,減少操作者非增值的時間,保證操作者的有效勞動。
7、建立基于信息化平臺精益管理績效考評機制
建立基于信息化平臺的精益管理績效考核機制通過系統(tǒng)論證和科學分析,明確以精益思想為指導建立生產(chǎn)管理績效考核機制,在高效、準確的信息源保障的基礎(chǔ)上,建立一套多層次、多角度的管理考核機制。為信息化平臺中的精益生產(chǎn)管理工作提供有力保障和實施管理的激勵機制。
建立生產(chǎn)有序、管理順暢,操作規(guī)范,士氣高昂、高質(zhì)量、低成本、短交期的作業(yè)現(xiàn)場;
為企業(yè)規(guī)劃設計一套由內(nèi)到外的形象升級,外觀視覺價值體現(xiàn)、內(nèi)在的管理內(nèi)涵體現(xiàn);
全員參與設備管理高產(chǎn)出和低成本運營,提升設備管理能力,維護能力,提高效率
構(gòu)建班組生產(chǎn)管理體系、循環(huán)評價、人才育成、持續(xù)改善、績效管理、文化養(yǎng)成體系;
提高產(chǎn)品質(zhì)量、降低生產(chǎn)成本、縮短交期、增加利潤,讓管理更系統(tǒng)科學,執(zhí)行力更強
對工廠的各個組成部分進行合理安排,以提高生產(chǎn)效率、降低成本、優(yōu)化物流、改善工作環(huán)境等