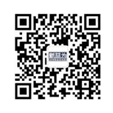
微信公眾號二維碼
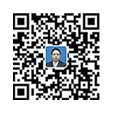
微信咨詢顧問二維碼
新益為精益生產(chǎn)咨詢公司概述:當(dāng)豐田掌門人提出公司所有新車型零部件的成本要降低30%的目標(biāo)時,遭到了很多部門的反對。然而,掌門人奉行“從干毛巾中擰出水來”的成本理念,要求各個部門通力協(xié)作,以更高的視角和創(chuàng)新思維來達(dá)成目標(biāo)。最終,他們實(shí)現(xiàn)了目標(biāo),并節(jié)省了100億美元。
降本增效
日本企業(yè)里的豐田,是成本控制方面的高手。他們的成本控制理念“從干毛巾中擰出水來”,一度成為企業(yè)成本管理上的至理名言。
大家知道,豐田是以消除浪費(fèi)、增加價值、持續(xù)改善的TPS豐田生產(chǎn)模式而聞名。然而,實(shí)際上在日本國內(nèi)及歐美各國,豐田首創(chuàng)的管理會計(jì)制度——目標(biāo)成本法所受到的重視并不亞于 JIT,甚而超越JIT。
目標(biāo)成本法是豐田汽車公司員工經(jīng)過幾十年努力探索出的杰作,是運(yùn)用科學(xué)管理原理和工業(yè)工程技術(shù)開創(chuàng)的具有日本文化內(nèi)涵的成本管理模式。
根據(jù)豐田公司的定義,目標(biāo)成本法是指從新產(chǎn)品的基本構(gòu)想、設(shè)計(jì)至生產(chǎn)開始階段,為降低成本及實(shí)現(xiàn)利潤而實(shí)行的各種管理活動。
歐美公司通常是先把產(chǎn)品設(shè)計(jì)出來,把成本計(jì)算出來,然后成本加上目標(biāo)利潤,就是產(chǎn)品的售價。這也是大多數(shù)企業(yè)定價的邏輯。
豐田的思路則截然不同,他們反其道而行之,先是測算出一個消費(fèi)者可以接受的價格,再減去企業(yè)的目標(biāo)利潤,最后得出目標(biāo)成本。
以汽車制造商為例,汽車的每一項(xiàng)功能都被視為產(chǎn)品成本的一個組成部分,從汽車的擋風(fēng)玻璃、引擎滑輪到引擎箱都事先制定一個目標(biāo)成本。
制定目標(biāo)成本,“這只是成本核算戰(zhàn)役的開始”。這一“戰(zhàn)役”的過程就是公司同外部供應(yīng)商之間,以及負(fù)責(zé)產(chǎn)品不同方面的各部門之間的談判過程。
最初的成本預(yù)算結(jié)果也許高出目標(biāo)成本的20%左右,或是一個更高的比例,但通過成本計(jì)劃人員、工程設(shè)計(jì)人員以及營銷專家之間妥協(xié)和利益權(quán)衡后,最終會得出一個與最初制定的目標(biāo)成本最為接近的計(jì)劃成本。
所以,豐田對成本控制的嚴(yán)苛可見一斑。也正是如此,使豐田經(jīng)常成為年度整車廠利潤最高的企業(yè)。
豐田也憑借這種優(yōu)秀的成本控制方法,大大提高了市場競爭力,并一躍成為歐美最強(qiáng)勁的競爭對手。
然而,即使一直在做精益,上世紀(jì)末,豐田公司仍然推出一個CCC21計(jì)劃(21世紀(jì)成本競爭力計(jì)劃),要求豐田在設(shè)計(jì)、生產(chǎn)、采購和固定費(fèi)用4個方面大規(guī)模壓縮成本,目標(biāo)是所有新車型關(guān)鍵部件的成本都要降低30%。
當(dāng)時這個計(jì)劃遭到很多部門的反對,大家認(rèn)為公司多年持續(xù)進(jìn)行合理化改善與QC小組活動,已改得很好了,很難實(shí)現(xiàn)這么大幅度的成本降低。
而當(dāng)時的掌門人渡邊捷照奉行“從干毛巾中擰出水來”的成本理念,要求各個部門通力協(xié)作,以更高的視角與創(chuàng)新思維來達(dá)成降低成本30%的目標(biāo)。
那么,最終豐田是如何實(shí)現(xiàn)的呢?
以車把手為例,如果將它的采購成本降低30%,或許大家普遍的做法是:有沒有尺寸小一點(diǎn)兒、厚度薄一點(diǎn)兒、材料差一點(diǎn)兒的類似產(chǎn)品呢?
其實(shí),這種方案不叫降本,叫降質(zhì)量。請大家記?。?降低采購成本,是不能犧牲質(zhì)量和庫存的。
豐田公司的做法和上述答案截然不同,它通過問以下問題,實(shí)現(xiàn)了采購成本下降30%。
1.公司有多少種車把手? 答案是35種。
2.從客戶感知到的價值,需要多少種才能滿足客戶的需求? 答案是3種。分別是高檔車專用車把手、中檔車專用車把手、低檔車專用車把手。
3.如果從35 種改成3種,有哪些成本節(jié)約? 答案是:35種車把手意味著35套設(shè)計(jì)、35套模具、35個從APQP (產(chǎn)品質(zhì)量先期策劃) 到PPAP (生產(chǎn)件批準(zhǔn)程序) 的驗(yàn)證過程,意味著35 套檢驗(yàn)規(guī)范、倉庫要留35個貨位、ERP里有35個料號、35種斷貨缺料的可能、35種產(chǎn)品生命周期結(jié)束后的呆滯物料、35種裝配錯誤的可能、要留35種售后備件庫……
當(dāng)縮減為3種時,意味著供應(yīng)商的生產(chǎn)量放大11倍多,由于規(guī)模效應(yīng),供應(yīng)商的固定成本被攤薄; 同時品類減少,操作工人換線時間變少,學(xué)習(xí)曲線發(fā)揮作用,單位產(chǎn)出時間縮短,產(chǎn)出效率提升。
另外供應(yīng)商品類少,越做越熟練,產(chǎn)品質(zhì)量也跟著提高。而對用戶而言,對車把手的感知,35種與3種并沒有太大區(qū)別。
所以,豐田組織了一個標(biāo)準(zhǔn)化、通用化小組,對車把手進(jìn)行標(biāo)準(zhǔn)化、通用化活動,于是成本就大大降低了。
那么,除了車把手,還有什么零部件可以進(jìn)行標(biāo)通化設(shè)計(jì)呢?
最后,豐田與供應(yīng)商共同努力,將豐田車空調(diào)排氣管種類由以前的27種降至4種,使相關(guān)成本降低了28%。但豐田還不滿足,它希望進(jìn)一步減少到3種。
看得見的地方盡量不一樣,看不見的地方統(tǒng)統(tǒng)一樣。通過上述類似活動,豐田成功地把關(guān)鍵零部件成本下降了30%,總共為豐田節(jié)約成本約100億美元。
豐田在眾多競爭對手市場份額下降,面臨巨額虧損的惡劣市場環(huán)境下,保持了快速的增長,市場份額穩(wěn)步攀升,而且創(chuàng)造了巨大的利潤,其中重要的舉措就是堅(jiān)持產(chǎn)品的多樣化和零部件的標(biāo)準(zhǔn)化相結(jié)合。
建立生產(chǎn)有序、管理順暢,操作規(guī)范,士氣高昂、高質(zhì)量、低成本、短交期的作業(yè)現(xiàn)場;
為企業(yè)規(guī)劃設(shè)計(jì)一套由內(nèi)到外的形象升級,外觀視覺價值體現(xiàn)、內(nèi)在的管理內(nèi)涵體現(xiàn);
全員參與設(shè)備管理高產(chǎn)出和低成本運(yùn)營,提升設(shè)備管理能力,維護(hù)能力,提高效率
構(gòu)建班組生產(chǎn)管理體系、循環(huán)評價、人才育成、持續(xù)改善、績效管理、文化養(yǎng)成體系;
提高產(chǎn)品質(zhì)量、降低生產(chǎn)成本、縮短交期、增加利潤,讓管理更系統(tǒng)科學(xué),執(zhí)行力更強(qiáng)
對工廠的各個組成部分進(jìn)行合理安排,以提高生產(chǎn)效率、降低成本、優(yōu)化物流、改善工作環(huán)境等