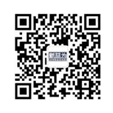
微信公眾號二維碼
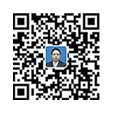
微信咨詢顧問二維碼
5S管理的真正目的是什么呢?新益為5S咨詢公司概述:5S管理是整理(Seiri)、整頓(Seiton)、清掃(Seiso)、清潔(Seikeetsu)和素養(yǎng)(Shitsuke)。這5個詞的縮寫。因為這5個詞日語中羅馬拼音的第一個字母都是“S”,所以簡稱為5S,開展以整理、整頓、清掃、清潔和素養(yǎng)為內容的活動,稱為5S活動。
5S咨詢
日本制造的工業(yè)產品一度質量低劣,只能在歐洲和美國的攤位上出售。但后來他們發(fā)明了“5S管理法”,養(yǎng)成了“認真對待每一件小事,按規(guī)定制作”的工作作風,徹底改變了日本人,為生產世界優(yōu)質產品奠定了堅實的基礎。
走進海爾的車間,很多企業(yè)界的人都會對那里的整潔和秩序印象深刻。對于一些領導視察或帶隊視察的企業(yè)來說,展開清理“迎接”,這樣的場面更是令人羨慕。有5S的貢獻,但海爾在5S的基礎上增加了一個“安全”,叫6S管理。海爾的工作坊還有醒目的“6S管理足跡”,是總結6S管理經驗的特殊場所,可見海爾人對6S管理的重視。
5S是現場管理的基石。5S可以創(chuàng)造一個“對”和“錯”一目了然的環(huán)境,讓每個人都必須約束自己的行為,久而久之,才能真正提高人的素質。
國內企業(yè)一直強調文明生產,其目的是希望企業(yè)有一個干凈、整潔、良好的工作環(huán)境。日本企業(yè)一直堅持做5S,規(guī)范現場和現在。幾十年來,我國企業(yè)亂七八糟的現象幾乎隨處可見,不按規(guī)定為所欲為的現象屢見不鮮。另一方面,日本企業(yè),無論是寫字樓還是廠房,真的是亮麗干凈,現場干凈整潔,給人的感覺是一切都在管理之中。抱著同樣的初衷,幾十年來中日企業(yè)現場管理的差距可謂天壤之別。“為什么會這樣?”,兩個原因:
第一,定位不同。國內許多企業(yè)管理者將清潔和清爽視為衛(wèi)生問題,這與生產不同。由于它們是兩回事,因此在忙碌時可以將自然工作放在一邊?;蛘哂猩霞夘I導來檢查工作,臨時做一次全面的清潔,給別人看。但日本企業(yè)管理者認為,5S是現場管理的基石,5S做得不好的企業(yè)不可能成為優(yōu)秀的企業(yè),因此會堅持把5S管理作為重要的管理原則。
第二,方法不同。許多國內企業(yè)熱衷于宣傳口號、文件和短期活動。他們似乎相信,在廠區(qū)多設置“員工十條”,可以改變一個人,提高他的素質。我們根本不能指望那些工作在臟亂差的環(huán)境中,沒有行為約束,能認真對待每一件小事的人。這種空洞的口號和不與日常工作相結合的運動,對提高人的素質沒有多大幫助。
另一方面,世界優(yōu)秀企業(yè)把5S作為現場管理必須具備的基本管理技術。5S管理明確規(guī)定了具體措施,如把什么物品放在哪里,如何放置,多少合適的數量,如何識別等,簡單有效,并融入到日常工作中。5S管理不僅是一種管理文化,也是現場科學管理的基礎。每天在“對”和“錯”一目了然的環(huán)境中工作,讓每個人都要約束自己的行為,久而久之,才能真正提高人的素質。
中國正在成為“世界工廠”,作為生產型企業(yè),僅靠目前低廉的勞動力成本是不可能與人長期競爭的。我們必須通過提高人的素質和灌輸科學的管理思想來培養(yǎng)良好的工作作風。海爾總裁張瑞敏對人的素質有個精彩的說法:“如果一個日本人訓練,讓他一天擦六次桌子,他一定會做;而一個中國人一開始擦六次,慢慢感覺4、5次就可以了,最后,他根本不擦拭它。”“中國人最大的問題是不認真,做事不妥,每天缺工,久而久之,就成了落后的頑疾”。
在20世紀40年代和20世紀50年代之前,日本制造的工業(yè)產品由于質量差,只能在歐洲和美國的攤位上出售。但他們發(fā)明了5S的管理方法,徹底改變了日本人,養(yǎng)成了“認真對待每一件小事,按規(guī)定制作”的工作作風。這種風格對于生產世界一流的優(yōu)質產品是不可或缺的。因此,中國企業(yè)要想與國外企業(yè)競爭,就應該像海爾一樣大力推行5S管理,提高人的素質。
一般企業(yè)管理者對5S的理解存在的兩大誤區(qū):1是把5S理解為清潔;2是沒有意識到5S的最終目的是提高人的素質。
5S管理的真正目的是什么呢?以上就是新益為5S咨詢公司的相關介紹,做好企業(yè)的5S咨詢工作就是為精益生產管理活動打下基礎,讓精益生產管理在企業(yè)中發(fā)展有一個良好的前提。
建立生產有序、管理順暢,操作規(guī)范,士氣高昂、高質量、低成本、短交期的作業(yè)現場;
為企業(yè)規(guī)劃設計一套由內到外的形象升級,外觀視覺價值體現、內在的管理內涵體現;
全員參與設備管理高產出和低成本運營,提升設備管理能力,維護能力,提高效率
構建班組生產管理體系、循環(huán)評價、人才育成、持續(xù)改善、績效管理、文化養(yǎng)成體系;
提高產品質量、降低生產成本、縮短交期、增加利潤,讓管理更系統科學,執(zhí)行力更強
對工廠的各個組成部分進行合理安排,以提高生產效率、降低成本、優(yōu)化物流、改善工作環(huán)境等